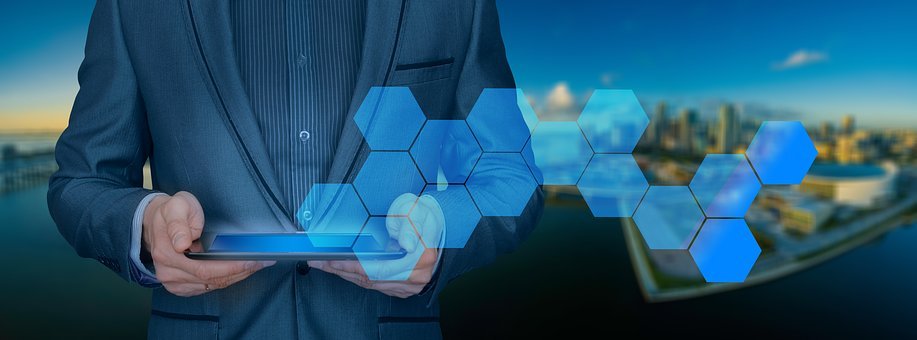
Learn how ultrasonic sensors work, how transmitters and receivers come into play, considerations for choosing an ultrasonic sensor, and their applications.
Due to their diverse capabilities, and flexibility, ultrasonic sensors make up a large part of the proximity sensing market, have continued to gain ground over the decades. In recent years, the demand for ultrasonic sensors has grown due to autonomous vehicles, robots, and drones. With this increased demand, the need to understand how they work, the best way for them to be used, and typical applications have similarly increased.
Ultrasonic sensors operate under the same principle as a bat using echolocation—emitting a high-pitched noise and timing how long it takes to reflect off an object and return. These noises, or chirps, are typically between 23 kHz and 40 kHz, where the term ultrasonic comes from.
How Ultrasonic Sensors Work
Using the room-temperature speed of sound in air, 343 m/s, we can quickly find the distance, keeping in mind that the noise travels in both directions—to and from the target. As a result, we get the following velocity-time equation:
With only straightforward multiplication and division in the equation, this calculation can be done with extremely simple and inexpensive microcontrollers.
Utilizing Beam Angles for Ultrasonic Transmitters
Much like a bat emits the ultrasonic chirp from its mouth and then hears the response with its ears, ultrasonic sensors also have a transmitter and receiver. Typically, these two are placed in close proximity to minimize any errors as the expectation is that the sound wave will be traveling in a straight line. Ultrasonic transceivers are another available option, where both the transmitter and receiver are combined into a single unit.
While acoustic waves travel in straight lines, they spread over time, which needs to be taken into consideration. With the spread and beam angle, these sound waves spread three-dimensionally, both vertically and horizontally.
Due to this, when reading datasheets about ultrasonic sensors, the detection area is given in beam width and angle, leaving the exact calculation up to the end-user. It should be noted that sometimes manufacturers provide the beam angle as the full angle of the beam while others provide the beam angle as the angle of deviation from the central point of the ultrasonic sensor.
As acoustic waves spread over distance, they correspondingly spread their energy as well. Usually, a narrower beam, with less spread, gives greater range. The flip side is that a wider beam usually has less range, but a wider detection area. The amount of energy initially put into the wave will play a dominant role in determining the range, regardless of beam angle. Application should determine beam angle and power input.
Considerations for Choosing an Ultrasonic Proximity Sensor
When choosing an ultrasonic sensor, there is more to consider than simply beam angle and detection angle.
Sensors can be bought individually, the transmitter and the receiver, or they can be purchased as a set already mounted on a PCB, typically with simple circuits that take care of the majority of the emission and detection work.
When the sensors are purchased separately, that circuitry can be custom-designed. This has the trade-off of requiring more design work but also yielding a great deal of flexibility.
There are also ultrasonic transceivers where both the transmitter and receiver are mounted into the same component, while typically more expensive, they use approximately half the footprint.
Strengths and Weaknesses of Ultrasonic Technology
While ultrasonic sensors are extremely popular, they are not perfect for every situation, and knowing their strengths and weaknesses will help match them to their most effective application.
Their strengths include:
- Being unaffected by the color or finish of the items being detected, including water or glass that are translucent or transparent.
- Flexible ranges, with minimum ranges down to a few centimeters and maximum ranges up to around five meters. Specialty ultrasonic sensors are also rated up to nearly 20 meters.
- Quick refresh rates, making multiple measurements every second.
- Relatively inexpensive due to their basic building materials.
- Well understood with predictable results due to being a mature technology.
- High precision with a typical error rate of 1% or less.
- Resistant to environments that suffer from high amounts of electromagnetic interference (EMI) and even acoustic interference.
A few of their weaknesses that should be taken into consideration that would make them less-than-ideal for an application include:
- Only provide a single point of data, making it difficult to create a full 2D or 3D picture without moving the sensor.
- Cannot provide feedback on the color or shape of an object being measured.
- Are dependent on temperature and humidity changing the speed of sound, reducing the precision of measurements.
- For embedded systems, they are larger than many available sensors though they are small enough for automotive or industrial applications.
- Dependent on sound, which means that the sensors must have a medium through which to measure. Therefore, they would not work in a vacuum.
Ultrasonic Sensor Applications
Automotive and industrial applications have been mentioned multiple times as they are extremely common applications of ultrasonic sensors, but they have many other potential uses.
Due to their ability to detect transparent materials, they are often used for liquid-level sensing. For liquids that need to remain pure or are toxic/corrosive, this can be beneficial as ultrasonic sensors are non-contact.
Object detection can be used in many industries including manufacturing facilities to detect people, boxes, vehicles, pallets, etc.. Of course, applications are only limited by the creativity of the system designer.
All images used courtesy of CUI Devices
Industry Articles are a form of content that allows industry partners to share useful news, messages, and technology with All About Circuits readers in a way editorial content is not well suited to. All Industry Articles are subject to strict editorial guidelines with the intention of offering readers useful news, technical expertise, or stories. The viewpoints and opinions expressed in Industry Articles are those of the partner and not necessarily those of All About Circuits or its writers.